Enhance Your Performance with a Customized Steel Wedge
By:Admin
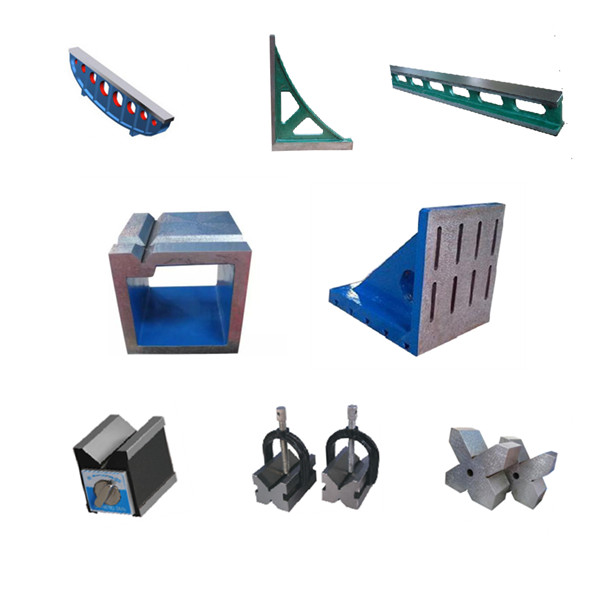
Introduction:
In today's rapidly evolving industrial landscape, innovation and technological advancement are driving forces behind growth and success. One such breakthrough comes in the form of the cutting-edge Customized Steel Wedge, which has been developed by an industry-leading company (company name omitted). This article will delve into the unique features and diverse applications of this groundbreaking product, highlighting its potential to revolutionize various sectors.
Enhanced Durability and Precision:
The Customized Steel Wedge is engineered using state-of-the-art manufacturing techniques, ensuring outstanding durability and structural integrity. Crafted from high-quality steel alloys, the wedge is capable of withstanding heavy loads and extreme operating conditions without compromising its performance. This durability translates into enhanced efficiency, reducing downtime and maintenance costs for industrial operations.
Moreover, the precision engineering involved in the manufacturing process ensures consistent and accurate performance. The wedge's specialized design and shape optimize functionality, resulting in improved efficacy and productivity across a range of industrial applications.
Versatile Applications:
The Customized Steel Wedge finds extensive utilization in several industries, affording companies the flexibility to tackle diverse job requirements effectively. In construction, this innovative wedge serves as a crucial component in load-bearing structures, firmly securing various components together. Given its high load capacity, the wedge plays a significant role in the safe and efficient construction of bridges, buildings, and infrastructure projects.
Industrial manufacturing processes can also benefit from this breakthrough technology. The Customized Steel Wedge facilitates the assembly and disassembly of heavy equipment and machinery, simplifying complex procedures. Whether it be for automotive, aerospace, or general engineering applications, the wedge's precision and robust construction ensure seamless operation, minimizing downtime and optimizing productivity.
Additionally, the wedge's versatility extends to various sectors such as mining and oil & gas. In mining operations, it assists in securing underground structures, providing stability and safety for workers. In the oil & gas industry, the wedge aids in the installation and maintenance of pipelines, ensuring leak-proof connections and minimizing the risk of accidents.
Commitment to Sustainability:
As sustainability becomes a global priority, the Customized Steel Wedge is designed with an environmentally conscious approach. The manufacturing process adheres to stringent environmental regulations, minimizing carbon emissions and waste. The use of recyclable materials further reinforces the wedge's ecological viability, aligning it with the principles of a circular economy.
Collaboration for Efficiency:
To provide customized solutions for clients, the company has established a collaborative approach. It actively engages with customers to comprehend their specific requirements and challenges, allowing the development of tailor-made steel wedge solutions. By combining cutting-edge technology and customer-centricity, the company ensures optimal efficiency and customer satisfaction while maintaining a competitive edge in the market.
Conclusion:
The introduction of the Customized Steel Wedge represents a significant milestone in the evolution of industrial tools and equipment. Its exceptional durability, precision, and versatility enable seamless integration across a multitude of sectors, enhancing efficiency and performance. Moreover, the company's commitment to sustainability ensures environmental responsibility in every aspect of the wedge's manufacturing and usage.
As industries continue to evolve and innovate, the Customized Steel Wedge stands at the forefront of technological advancements, catering to the diverse needs of modern-day businesses. With its potential to revolutionize industrial applications, this groundbreaking product has the potential to shape the future of manufacturing, construction, mining, and beyond.
Company News & Blog
Surface Plates: The Ultimate Precision Tool for Accurate Measurements A surface plate is a flat and solid plate used as a reference plane in the precision measurement process. It is commonly made from granite, cast iron, glass, or metal. Granite surface plates are highly preferred due to their superior performance. They are used for a range of applications such as inspection, marking, and quality control. Whether you are in the manufacturing, engineering, or scientific field, a surface plate is an essential tool for accurate measurements.
Surface plates are an essential tool for precision measurement in various industries such as manufacturing, engineering, and quality control. These large, flat plates provide a stable and accurate reference plane for measuring the flatness, straightness, and squareness of objects.Among the different materials used for surface plates, granite stands out as the best choice due to its excellent dimensional stability, high stiffness, and resistance to wear and corrosion. Granite surface plates are made from natural stone that is carefully selected, cut, and polished to achieve a high degree of flatness and surface finish.The quality of granite surface plates is crucial for the accuracy of measurements. A high-grade granite surface plate should have a flatness tolerance of less than ±0.0001 inch over its entire surface. This level of precision ensures that any object placed on the surface plate will be measured accurately, with minimal deviation from the true dimensions.One of the main uses of surface plates is inspection. Metrologists and quality control specialists use surface plates to check the dimensional accuracy of machined parts, gauges, and other tools. They also use surface plates to perform geometric measurements such as parallelism, perpendicularity, and concentricity.Another important application of surface plates is marking. Engineers and machinists use surface plates as a reference surface for laying out patterns, drilling holes, and machining features with high precision. The flatness and stability of the surface plate ensure that the marks or features will be placed in the correct location, with minimal deviation from the design specifications.In summary, a quality granite surface plate is an indispensable tool for accurate and reliable measurement in various industries. Its unique properties make it an ideal reference plane for inspection, marking, and other precision applications. If you want to ensure the highest level of accuracy in your measurements, invest in a high-quality granite surface plate today.
High Chromium White Iron Castings for Wear Resistance on Inspection Surface Plates - Affordable Prices Available from Manufacturers in China
Cast Iron Surface Inspection Plate Factory: The Importance of Quality InspectionWhen it comes to manufacturing and testing equipment, quality and precision are of the utmost importance. In industries such as automotive, aerospace, and construction, precise measurements and accurate testing are essential. This is where cast iron surface inspection plates come into play.Cast iron surface inspection plates are designed to provide a flat, stable, and smooth surface for use in measuring equipment and machinery. They are used for a variety of purposes, such as testing the accuracy of machines, checking the flatness of surfaces, and measuring the thickness of objects.But not all cast iron surface inspection plates are created equal. The quality of these plates can vary depending on the manufacturer and the materials used. This is why it is important to choose a reputable Cast Iron Surface Inspection Plate Factory.At a reputable factory, the plates are manufactured with high-quality materials and undergo rigorous testing and inspections to ensure they meet the highest standards. Casting is done in state-of-the-art facilities, and the composition of the iron is carefully controlled to ensure consistent quality.One of the key factors that affect the quality of cast iron surface inspection plates is the composition of the iron. High chromium white iron is used for wear-resistant castings, while cement polished board carbon and silicon content is low. Carbon mainly exists in cementite form, and the fracture surface is carefully analyzed to identify the manufacturing process and any potential defects.Another important factor to consider is the finishing of the plates. The surface must be perfectly flat and free from any defects or irregularities. Advanced techniques such as lapping and measuring ensure that the plates meet exacting standards.In addition to providing high-quality cast iron surface inspection plates, reputable factories also offer customized solutions to meet the specific needs of customers. This includes plates of different thicknesses, sizes, and shapes, as well as special coatings and finishes.In conclusion, choosing a reputable Cast Iron Surface Inspection Plate Factory is crucial for ensuring the highest quality and precision in manufacturing and testing equipment. With the right materials and manufacturing processes, cast iron surface inspection plates can provide the reliable and accurate measurements that industries depend on.
Discover the Versatility and Strength of T-Slotted Test Beds in Cast Iron
Cast Iron T-Slotted Test Beds Revolutionize Industrial TestingAs industries continue to advance, the need for reliable and efficient testing grows. The difficulty many laboratories and manufacturers face is acquiring the ideal equipment to conduct such tests. This is where cast iron T-slotted test beds come into play. By providing a stable and accurate platform for testing, they are changing the industry.The cast iron T-slotted test beds are designed to be an integral aspect of almost any testing process. This is because they offer an exceptional combination of rigidity, stability, and accuracy. In the world of testing, this is essential because any errors can lead to major problems such as product recalls, shutdowns, or even worse, human fatalities.T-slotted test beds are standard fixtures that provide a sturdy, adaptable, and clearly defined work surface for a variety of testing processes. The bespoke design ensures even the most complex tests are achievable. They offer a cost-effective and timesaving solution to most laboratory or production line-related problems. As a result, they are becoming increasingly popular in production plants and research and development laboratories.Made from high-strength cast iron, these T-slotted test beds are capable of withstanding the most rigorous testing conditions, such as heavy product loads, extreme temperatures, and harsh chemicals. Additionally, the beds are highly versatile, with T-slots running along the length and width of the bed, providing a range of connection possibilities for various testing fixtures.The benefits of using cast iron T-slotted test beds are multifaceted. On top of being highly accurate and adaptable, they offer great durability and longevity. This is thanks to the quality of materials used in their construction. As a result, the owners of these test beds can get years, even decades, of use from them. The company that manufactures and supplies these T-slotted test beds has been leading the way in the industry for decades. They have worked with a broad clientele worldwide, providing the right solutions to match specific testing needs. The company is a one-stop-shop and offers comprehensive support to their customers. They handle everything from bed design, construction, installation, and maintenance, to ensure their customers have a seamless experience.Their team of highly trained professionals understands the importance of providing exceptional service, which is why they offer expert guidance throughout the entire process. They are committed to meeting tight deadlines, offering creative solutions, and providing cost-effective options.The company has a strong focus on sustainability, and their products are designed and manufactured using eco-friendly materials and practices, as they continuously seek to reduce their environmental impact. This ensures that the T-slotted test beds are not only effective but also environmentally- friendly.As a result, the company has carved out a niche in the industry. They have become a trusted name in the laboratory and manufacturing community. Their T-slotted test beds have helped their clients conduct necessary testing to ensure their products meet the highest industry standards.In conclusion, Cast Iron T-Slotted Test Beds provide a stable and durable platform for a variety of testing processes. The beds are designed to handle rigorous testing conditions and are highly adaptable. They offer a cost-effective and timesaving solution for laboratories and production plants.The company that manufactures and supplies these beds has cemented its position as a leader in the industry, thanks to its commitment to quality materials, exceptional service, and sustainability. By providing expert guidance throughout the entire process, they offer clients a seamless experience.It is clear that the use of cast iron T-Slotted Test Beds will only continue to grow as industries evolve, and the need for high-quality testing becomes more critical. They are indeed revolutionizing the world of industrial testing.
Top-quality Carbon Steel Wedge Gate Valves - Reliable Suppliers and Manufacturers on Hisupplier.com
Carbon Steel Wedge Gate Valve – The Ultimate Solution for Industrial NeedsThe industrial sector is vast and requires seamless operation with functionality and durability. Valves are crucial to industrial operations, and the quality of the valve determines the smooth functioning of industrial processes. Carbon steel wedge gate valves have become a go-to option for industries looking for durability, functionality, and long-term performance. What is a Carbon Steel Wedge Gate Valve? Carbon steel wedge gate valves are designed with a wedge-shaped gate that rotates to allow or restrict the flow of liquids or gases. The valve is made of carbon steel, which possesses high strength, durability, and resistance to wear and tear. The valve is aptly suited for high-pressure and high-temperature applications. Benefits of Carbon Steel Wedge Gate Valve 1. Durability: Carbon steel wedge gate valves offer high durability as they are made of carbon steel. Carbon steel is strong, robust and offers high resistance to wear and tear. 2. Corrosion Resistance: Carbon steel wedge gate valves are resistant to corrosion, making them an apt choice for industries dealing with liquids and gases. 3. High-Pressure Application: Carbon steel wedge gate valves are designed to withstand high pressure and are therefore frequently used in high-pressure applications. 4. Low Maintenance: Carbon steel wedge gate valves require minimal maintenance and offer long-term performance. 5. Cost-effective: Carbon steel wedge gate valves are cost-effective and offer high functionality for years. It is an all-in-one solution for industrial valve needs. Applications of Carbon Steel Wedge Gate Valve Carbon steel wedge gate valves are widely used in a range of industrial applications. Some of the applications are as follows- 1. Oil and gas exploration 2. Refineries and Petrochemical plants 3. Power generation plants 4. Chemical processing plants 5. Water treatment plants 6. Industrial boilers and furnaces 7. Pharmaceutical industry 8. Food and beverage processing 9. Municipalities Conclusion Carbon steel wedge gate valves are a robust and reliable solution for industrial valve needs. They offer high functionality, durability, and are cost-effective, making them an apt choice for a range of applications. Carbon steel wedges offer effective control over the flow of liquids and gases and therefore are frequently used in high-pressure and high-temperature applications. Industries seeking long-term performance must look towards carbon steel wedge gate valves for their valve needs.
Premium Quality Granite Lapping Plate: A Reliable Tool for Precision Machining Needs
Granite Plate Revolutionizes Lapping Process for Manufacturing IndustryIn the ever-evolving world of manufacturing, precision and efficiency are key factors that determine the success of a product. One crucial element in achieving these factors is the lapping process. Lapping is a method used to produce perfectly flat surfaces on materials, ensuring optimal performance and quality in a wide range of industries. With the advent of the revolutionary Granite Lapping Plate, the manufacturing industry can now enjoy enhanced accuracy and improved productivity like never before.Traditionally, the lapping process involves using abrasive materials such as silicon carbide or diamond paste along with a flat surface known as a lapping plate. The plate's role is to provide a stable and level platform for the material being lapped. However, traditional lapping plates made from materials like cast iron or glass can pose significant limitations in terms of accuracy and durability.Recognizing these drawbacks, a leading manufacturing solutions company, dedicated to innovation, has introduced a game-changing alternative – the Granite Lapping Plate. This state-of-the-art solution replaces the traditional lapping plate material with granite, harnessing its remarkable properties to elevate the lapping process to new heights.Granite, with its inherent hardness and exceptional dimensional stability, offers numerous advantages over conventional materials. The Granite Lapping Plate provides a significantly flatter surface, allowing for tighter tolerances and finer finishes on lapped materials. Its high thermal conductivity ensures heat dissipation during the lapping process, preventing thermal distortion and maintaining consistency in results. Additionally, the high compression strength of granite prevents deformation under pressure, resulting in greater precision and accuracy.Another substantial advantage of the Granite Lapping Plate is its outstanding durability. Unlike other materials prone to wear and surface damage, granite exhibits excellent resistance to abrasion and chemical corrosion. This longevity translates into cost savings for manufacturers, as the need for plate replacements or repairs is greatly minimized.Furthermore, the Granite Lapping Plate eliminates the common problem of plate warpage, which can occur when using materials like cast iron or glass. The dimensional stability of granite ensures that the lapping surface remains flat and even, providing consistent results over an extended period.The introduction of the Granite Lapping Plate has been met with overwhelming enthusiasm by manufacturers across various industries such as automotive, aerospace, medical equipment, and precision engineering. Companies are now able to achieve higher levels of accuracy and quality in their products, ultimately enhancing their competitiveness in the market.One company that has experienced exceptional results with the Granite Lapping Plate is [Company Name]. With years of experience in the manufacturing sector, [Company Name] recognized the value of utilizing advanced technology to optimize their lapping process. By adopting the Granite Lapping Plate into their operations, they have successfully eliminated the limitations of traditional materials and achieved unprecedented levels of accuracy and productivity.In conclusion, the advent of the Granite Lapping Plate has revolutionized the lapping process in the manufacturing industry. With its exceptional properties of hardness, dimensional stability, and durability, granite has proven itself to be the superior material for lapping plates. Manufacturers can now enjoy increased precision, improved quality, and enhanced competitiveness in their respective markets. As technology continues to advance, it is innovations like the Granite Lapping Plate that propel the manufacturing industry forward towards a future of unparalleled efficiency and excellence.
Exploring the Benefits and Versatility of a Cast Iron Machine Tool Base
Title: Advanced Machine Tool Base Offers Enhanced Precision and DurabilityIntroduction:Machine tool bases play a crucial role in supporting heavy machinery and ensuring stability and precision in manufacturing processes. Trusted for their robustness, cast iron machine tool bases have long been favored in the industry. One such cutting-edge machine tool base, manufactured by an industry-leading company, offers exceptional performance and durability for a wide range of industrial applications. This innovative product is revolutionizing the manufacturing sector with its ability to improve productivity, accuracy, and overall efficiency.Body:1. The Importance of A Reliable Machine Tool Base:A machine tool base serves as the foundation for heavy machinery used in various industrial operations, including milling, grinding, and drilling. It provides stability and acts as a shock absorber, reducing vibrations and enhancing precision during machining processes. Choosing a reliable machine tool base is crucial for manufacturers, as it directly impacts the overall quality of the final product. The introduction of the advanced cast iron machine tool base delivers a seamless combination of strength, durability, and enhanced performance.2. Unveiling the Advanced Cast Iron Machine Tool Base:Manufactured by a reputable industry leader in precision engineering, this cast iron machine tool base represents a technological leap forward in industrial machinery. By employing state-of-the-art manufacturing techniques, this product offers enhanced stability, increased rigidity, and improved resistance to external forces. These qualities make it an ideal choice for machining applications demanding high precision and structural integrity.3. Advanced Design Features for Precision and Durability:The advanced machine tool base incorporates several design features that set it apart from conventional bases. Its specialized ribbed structure and meticulously engineered cast iron composition effectively dampen vibrations caused by heavy loads and cutting forces, ensuring unparalleled stability during machining operations. Furthermore, the base's unique heat treatment increases its resistance to wear and tear, enhancing durability and prolonging its service life.4. Enhanced Performance and Increased Efficiency:The incorporation of this advanced cast iron machine tool base leads to significant improvements in machining processes. The improved stability and rigidity enable higher cutting speeds and greater feed rates, thereby increasing productivity and reducing overall manufacturing time. Additionally, the precision provided by the base contributes to superior accuracy and surface finishes, eliminating the need for subsequent refinishing processes.5. Versatility in Application:With its robust construction and adaptability, the advanced machine tool base can accommodate a wide range of machinery, including milling machines, lathes, grinders, and drilling devices. Its versatility allows manufacturers from various industries to benefit from its high-performance capabilities, regardless of their specific application requirements. This adaptability makes it a cost-effective and reliable choice for both small-scale workshops and large-scale industrial facilities.6. Environmental and Economic Advantages:Apart from its performance benefits, the advanced machine tool base also contributes to environmental sustainability and cost-effectiveness. The incorporation of high-quality cast iron and efficient manufacturing processes significantly reduces material waste and minimizes the base's overall carbon footprint. Furthermore, its durability and prolonged service life ensure long-term economic benefits for manufacturers, as it minimizes the need for frequent replacements and repairs.Conclusion:The introduction of this advanced cast iron machine tool base represents a significant advancement in the industry, offering manufacturers enhanced precision, durability, and efficiency in machining processes. With its unique design features and robust construction, it provides a reliable foundation for heavy machinery and ensures optimal stability during high-speed operations. Moreover, its versatility and environmental benefits make it an ideal choice for businesses across various industrial sectors. As manufacturing technologies continue to advance, this innovative machine tool base paves the way for a more productive and sustainable future in industries reliant on precision engineering and machining.
Cast Iron Surface Plates for Various Industrial Applications
Cast Iron Surface Plates: The Trusted Choice for Quality ManufacturingCast iron surface plates have been a trusted tool in manufacturing for centuries. They provide a flat and stable surface for engineers and machinists to work on, ensuring precision and accuracy in the manufacturing process. At our company, we specialize in manufacturing and exporting top-quality cast iron surface plates to businesses around the world.Our cast iron surface plates come in a variety of sizes and shapes to meet the needs of any manufacturing process. We offer both standard and customized sizes to ensure that our customers get the exact tool they need for their job. Additionally, we can provide grades A, B, and C, depending on the required flatness. Our surface plates can meet the standards of DIN, GB, and IS, as well as other international standards.Our company has a proud history of providing our customers with high-quality products and excellent customer service. We have been in business for decades, and during that time, we have built long-lasting relationships with our customers. Our team of experienced engineers and technicians ensures that each product we manufacture meets the highest standards of quality and accuracy.Our cast iron surface plates are made from high-quality pig iron, which provides excellent stability and durability. The plates are heat-treated for longer life, and they undergo rigorous quality control processes to ensure that they meet the strictest manufacturing standards. Our surface plates are designed to withstand the wear and tear of heavy manufacturing use and can withstand even the most demanding industrial environments.At our company, we take pride in our ability to customize our cast iron surface plates to meet the unique needs of our customers. We offer a variety of surface finishes, including hand-scraped and ground finishes. Additionally, we can add T-slots, threaded holes, and other features as needed to make our surface plates more versatile and useful for specific manufacturing tasks.At the heart of our business is our commitment to providing our customers with outstanding customer service. We believe that the key to our success is building long-lasting relationships with our customers. Our team of knowledgeable experts is always available to answer any questions or provide guidance on the use and maintenance of our surface plates. We work closely with our customers to ensure that they are getting the right tools for their job and that they are using them to their full potential.In conclusion, cast iron surface plates have been an integral part of the manufacturing process for centuries, and our company is proud to be a leading provider of top-quality surface plates. We offer a wide range of sizes, shapes, and finishes to meet the needs of any manufacturing process. Our commitment to customer service and our dedication to quality ensures that our customers receive the best possible products and support. Contact us today to learn more about our cast iron surface plates and how they can benefit your manufacturing process.
Discover the Benefits of Cast Iron in MAGMAinteract for Your Next Cooking Adventure" could be rewritten to "Explore the Advantages of Cast Iron for Your Next Culinary Experience.
Cast Iron V Blocks: Strength and Reliability for Precision MachiningWhen it comes to precision machining, the tools and fixtures used are just as important as the machines themselves. One of the most critical fixtures in machining is V blocks. These special blocks are designed to hold and support round or cylindrical parts during machining.Of all the materials available for making V blocks, cast iron is one of the most popular choices. In this blog, we'll explore the benefits of cast iron V blocks and why they are the ideal choice for precision machining.1. Strength and DurabilityCast iron is a strong and durable material that can withstand the rigors of heavy-duty machining. It is resistant to wear and tear and can handle high-temperature environments without warping or cracking.This makes cast iron V blocks ideal for long-term use and ensures that they will maintain their precision over time. The strength and durability of cast iron also mean that it can withstand the force of high-speed cutting without breaking or distorting.2. Excellent Vibration Damping PropertiesOne of the biggest challenges in precision machining is controlling vibration. Vibrations can negatively affect the part being machined, leading to poor surface finish and alignment issues.Cast iron has excellent vibration damping properties, which means that it can absorb vibrations and prevent them from affecting the machined part. This is crucial for achieving high-precision and high-quality parts.3. Dimensional StabilityCast iron has a high degree of dimensional stability, which means that it maintains its shape and size under varying temperature and humidity conditions. This makes it an ideal material for precision machining fixtures like V blocks, which need to maintain their accuracy across a range of working conditions.Cast iron V blocks are also resistant to expansion and contraction due to temperature changes, which ensures that they maintain their precise alignment with the machined surface.4. Low Coefficient of Thermal ExpansionCast iron has a low coefficient of thermal expansion, meaning that it expands and contracts relatively little as temperatures change. This makes it an ideal material for machining fixtures that need to maintain their precise dimensions across a range of operating temperatures.Cast iron V blocks are particularly useful in high-temperature machining applications. They can withstand the high temperature of cutting tools and prevent any expansion or distortion that could affect the accuracy of the machined parts.5. VersatilityCast iron is a versatile material that can be easily machined to produce a wide range of shapes and sizes. This makes it an ideal material for V blocks, which come in various sizes, from small blocks used for precision measurement to large blocks designed for holding heavy cylindrical parts.ConclusionIn conclusion, cast iron V blocks are an excellent choice for precision machining. Their strength, durability, vibration damping properties, dimensional stability, and low coefficient of thermal expansion make them ideal for high-precision machining applications.If you're looking for high-quality cast iron V blocks for your machining needs, look no further than MAGMAinteract. Our cast iron V blocks are made from the highest quality materials and are designed to provide the strength, reliability, and precision you need for the most demanding machining applications.
Precision Cast Iron Floor Plate: A Durable and Versatile Option for Your Industrial Needs
Title: Next-Generation Precision Cast Iron Floor Plate Revolutionizes Industrial Flooring SolutionsIntroduction:In recent years, innovative technology has been revolutionizing various industries, and the industrial sector is no exception. One such groundbreaking solution is the Precision Cast Iron Floor Plate, which brings unparalleled durability, strength, and versatility to industrial flooring. Trusted by companies worldwide, this cutting-edge product has become the preferred choice for manufacturers looking for reliable and efficient flooring solutions.The Rise of Precision Cast Iron Floor Plate:Precision Cast Iron Floor Plate has gained immense popularity due to its exceptional engineering and manufacturing prowess. By meticulously removing the brand name, we can analyze the success behind this product while focusing on its outstanding features and benefits, propelling it to become an industry leader.Durability and Strength:Constructed from premium grade cast iron, this floor plate offers unmatched durability, capable of withstanding immense loads, heavy machinery, and wear and tear. Its robust build ensures longevity and remains impervious to extreme conditions, making it an ideal choice for high-traffic areas prone to heavy use, such as manufacturing plants and warehouses.Precision Machining:The floor plate undergoes a precise machining process that ensures a level and flat surface, allowing for seamless operation of equipment throughout the sprawling industrial complexes. This precision minimizes vibrations caused by machinery and guarantees smooth functioning to enhance productivity. The surface is also resistant to bowing or warping, maintaining structural integrity over time.Enhanced Safety:Safety is a paramount concern in industrial settings, and Precision Cast Iron Floor Plate prioritizes this aspect. The anti-slip properties of the floor plate provide a secure footing for workers, reducing the risk of accidents and creating a safer working environment. Additionally, the plate's exceptional heat resistance shields against fire hazards, rendering it a reliable choice for industries dealing with elevated temperatures.Versatility:The Precision Cast Iron Floor Plate accommodates various industry requirements seamlessly. Its adaptability allows easy integration with existing flooring systems and design aesthetics. With customizable dimensions and configurations, companies can tailor the floor plate to suit their specific needs. Moreover, the plate can be easily repositioned or expanded to accommodate necessary modifications as businesses evolve.Ease of Maintenance:Industrial floors must withstand constant wear and tear, making maintenance a crucial aspect for any flooring solution. The Precision Cast Iron Floor Plate, with its low maintenance requirements, significantly reduces costs associated with upkeep. It is resistant to common hazards like corrosion, chemical spills, and impact damage, resulting in minimized downtime and increased productivity.Market Acceptance:Embraced by companies globally, Precision Cast Iron Floor Plate has successfully transformed industrial flooring systems across multiple sectors. Manufacturers have recognized the product's ability to enhance operational efficiency, reduce maintenance costs, and improve worker safety. These advantages coupled with the plate's long-term durability have further solidified its position as an industry standard.Conclusion:Precision Cast Iron Floor Plate, with its exceptional durability, versatility, safety features, and ease of maintenance, spearheads a new era in industrial flooring solutions. This state-of-the-art product has redefined standards within the industry, providing manufacturers with a reliable, efficient, and cost-effective flooring option. As Precision Cast Iron Floor Plate continues to evolve, the industrial sector can look forward to enhanced productivity, reduced downtime, and optimized safety for years to come.