Versatile Welding Table System for Efficient Workholding
By:Admin
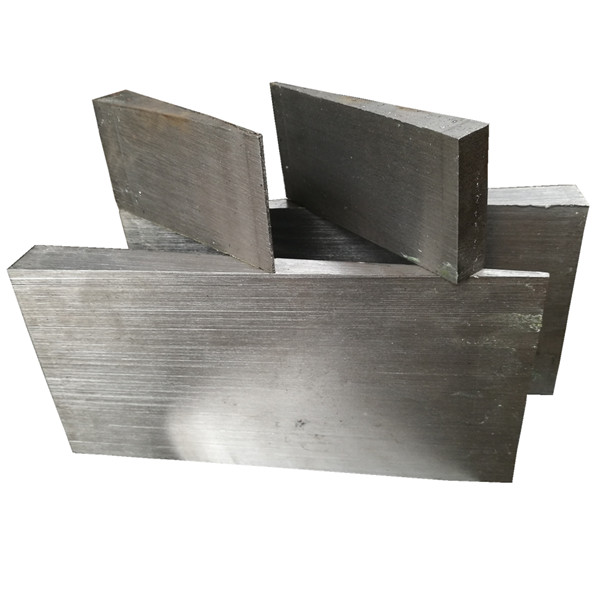
Welding has always been an essential part of various industries, from construction to manufacturing. Welders often face challenges in achieving precision and efficiency in their work. However, the introduction of the innovative Modular Welding Table System has revolutionized the welding industry, offering a game-changing solution to these challenges.
This cutting-edge welding system is the brainchild of a leading manufacturing company (Company Name), widely recognized for its commitment to engineering excellence and product innovation. With a strong emphasis on quality and performance, (Company Name) has continuously strived to develop advanced solutions that cater to the evolving needs of the welding industry.
The Modular Welding Table System is a testament to (Company Name’s) dedication to providing welders with state-of-the-art tools that enhance productivity and accuracy. This innovative system consists of a versatile range of modular welding tables, clamping systems, and accessories, all designed to provide a flexible and efficient work surface for welding applications.
One of the key features of the Modular Welding Table System is its modular design, which allows welders to easily assemble and reconfigure the tables to accommodate various welding projects. This flexibility is a game-changer for welders, as it eliminates the need for multiple fixed welding tables, saving time, space, and resources.
Furthermore, the welding tables are equipped with a grid of bore holes, enabling welders to position and secure workpieces with precision using a range of clamping devices. This level of customization and adaptability ensures that welders can achieve the highest level of accuracy in their work, ultimately resulting in top-quality welds.
The Modular Welding Table System also boasts compatibility with a range of accessories, including stop bars, angle brackets, and magnetic holders, further enhancing its functionality and versatility. These accessories provide welders with the necessary tools to streamline their workflow and tackle a wide array of welding tasks with ease.
In addition to its innovative design, the Modular Welding Table System prioritizes durability and stability, ensuring that it can withstand the rigors of industrial welding operations. The tables are constructed from high-quality materials, offering a robust and reliable work surface that can withstand the intense heat and pressure associated with welding.
The introduction of the Modular Welding Table System has been met with widespread acclaim within the welding industry, as it addresses many of the challenges that welders face on a daily basis. Welders have praised the system for its ability to streamline their workflow, improve precision, and ultimately enhance the quality of their welds.
Furthermore, (Company Name) has provided comprehensive training and support for welders looking to integrate the Modular Welding Table System into their operations. This commitment to customer satisfaction exemplifies (Company Name’s) dedication to providing holistic solutions that empower welders to achieve their best work.
As the demand for high-quality welding solutions continues to grow, (Company Name) remains at the forefront of innovation, continuously developing new technologies and solutions that push the boundaries of what is possible in the welding industry. The Modular Welding Table System is a shining example of (Company Name's) commitment to engineering excellence and its determination to drive positive change in the welding industry.
In conclusion, the Modular Welding Table System has reshaped the landscape of the welding industry, setting a new standard for precision, efficiency, and versatility. With its innovative design, durability, and compatibility with a range of accessories, this system has empowered welders to elevate their craft and deliver top-quality welds with ease. As (Company Name) continues to lead the way in engineering advancements, the welding industry can look forward to a future filled with groundbreaking solutions that push the boundaries of what is possible.
Company News & Blog
T-Slotted Cast Iron Floor Plates: Ideal for Engineering Industry Applications
Cast iron has been used in the manufacturing industry for centuries as it is known for its durability, strength, stability, and resistance to wear and tear. Cast iron is one of the most common materials used in machine bases, worktable beds, and other types of equipment that require rigid and stable support.One great example of the use of cast iron in the manufacturing industry is the JASH Cast Iron T-Slotted Floor Plates. These floor plates are designed and manufactured by JASH, a leading manufacturer and supplier of precision machines and cast iron products. JASH Cast Iron T-Slotted Floor Plates are used in engineering industries as rigid bases for layout, marking, inspection, testing, assembly work, large fixtures, special tooling, and production set-ups.These floor plates are suitable for a wide range of applications in diverse engineering industries, including automotive, aerospace, defense, railway, power generation, and heavy engineering. Their versatility and sturdiness make them the preferred choice for industrial processes that require high accuracy, repeatability, and stability.The JASH Cast Iron T-Slotted Floor Plates are designed to provide a solid, level, and stable base for various industrial applications. The refined cast iron construction provides a high degree of rigidity, vibration damping, and thermal stability. These floor plates are precisely engineered to ensure flatness within ±0.05mm/metre. The T-slots on the surface of the plates help in easy positioning and clamping of workpieces and fixtures.The T-slots on the plates are machined to exacting standards to ensure optimal alignment and smooth motion of workpieces and fixtures. The slots are spaced at regular intervals and are available in different sizes to suit various applications. The T-slots also allow easy attachment and clamping of accessories and tooling, like hold-down bolts, clamps, vices, and chucks.The JASH Cast Iron T-Slotted Floor Plates are available in different sizes, shapes, and configurations to suit various industrial requirements. The plates are available in rectangular, square, and round shapes in sizes ranging from 200mm x 200mm to 4000mm x 4000mm. The plates can be customized to include additional features like holes, pockets, bosses, and pedestals to suit specific production needs.JASH has been a trusted name in the manufacturing and engineering industries for over five decades. The company has a state-of-the-art manufacturing facility equipped with the latest machinery, tools, and systems to produce high-quality and high-performance cast iron products. JASH has a team of highly skilled and experienced engineers, technicians, and support staff who ensure that every product meets the highest international standards of quality and reliability.Apart from Cast Iron T-Slotted Floor Plates, JASH also manufactures other precision machinery and cast iron products like Angle Plates, Box Angle Plates, Granite Surface Plates, and T-Slotted Angle Plates. JASH products are exported to over 30 countries worldwide, and the company has a strong global presence through its network of dealers and distributors.In conclusion, JASH Cast Iron T-Slotted Floor Plates are a reliable and durable solution for industrial processes that require accurate and stable support. Their versatility and precision make them ideal for a wide range of applications in various engineering industries. JASH's commitment to quality, innovation, and customer satisfaction ensures that its products meet the highest standards of performance and reliability. With JASH, you can be assured of getting the best cast iron products that will last for years to come.
Exploring the Versatility and Durability of Cast Iron Machine Tool Bases
Title: Cast Iron Machine Tool Base Revolutionizes Precision ManufacturingIntroduction:In today's competitive manufacturing industry, precision and accuracy are paramount. Enter the cast iron machine tool base, a game-changer that has taken the manufacturing world by storm. By combining heavy-duty cast iron construction with cutting-edge technology, this innovative tool base has revolutionized the way precision components are produced. In this article, we explore the features and capabilities of the cast iron machine tool base and the company that is pioneering its development.I. Background:With advancements in technology and increasing market demands, manufacturing industries have been seeking ways to enhance precision and efficiency in production processes. The cast iron machine tool base, developed by a renowned manufacturing solutions provider, has emerged as a groundbreaking solution.II. Features and Benefits:The cast iron machine tool base boasts several features that set it apart from traditional alternatives. Firstly, the use of cast iron provides exceptional stability and vibration absorption, resulting in enhanced precision. The robust construction ensures minimal distortion even under heavy loads, providing a stable foundation for tooling and machinery.Additionally, the base incorporates state-of-the-art technology that enables precise positioning and accurate machining. Through advanced calibration systems and built-in sensors, the machine tool base can monitor and adjust for any environmental variations, ensuring consistent and high-quality production.Moreover, the base's modular design allows for easy customization and flexibility, providing manufacturers with the versatility to adapt the tool base to their specific needs. This feature ensures that the machine tool base can be integrated seamlessly into existing production lines, minimizing downtime and maximizing productivity.III. Applications:The cast iron machine tool base finds applications across a wide range of industries that require precision manufacturing. From automotive and aerospace to electronics and medical, this tool base provides the foundation necessary to achieve the tight tolerances demanded by these sectors.In the automotive industry, for example, the cast iron machine tool base is used in the production of engine components, transmissions, and chassis parts. Its stability and precision help manufacturers meet stringent quality standards, while also improving overall productivity.Furthermore, in the aerospace industry, where absolute precision is of utmost importance, the machine tool base plays a critical role in the production of aircraft parts and components. By eliminating vibrations and offering accurate positioning, aviation manufacturers can ensure the highest levels of safety and performance.IV. Company Introduction:Behind this groundbreaking invention lies a reputable manufacturing solutions provider, known for its dedication to technological advancements in the industry. With a profound understanding of the challenges faced by modern manufacturers, this company has consistently delivered innovative solutions that enhance efficiency and productivity.Committed to research and development, the company invests heavily in cutting-edge technologies, ensuring that its products remain at the forefront of the market. Backed by a team of experienced engineers and technicians, the company continues to push boundaries, revolutionizing precision manufacturing processes.V. Conclusion:The cast iron machine tool base, developed by this pioneering manufacturing solutions provider, represents a significant advancement in the field of precision manufacturing. Its unique features, such as cast iron construction, advanced technology, and modular design, make it an invaluable asset for industries that demand accuracy and efficiency.As manufacturers strive for higher quality standards and increased productivity, the cast iron machine tool base stands as a testament to the power of innovation. With its ability to provide stability, accuracy, and adaptability, this tool base exemplifies the future of precision manufacturing.
High Chromium White Iron Castings for Wear Resistance on Inspection Surface Plates - Affordable Prices Available from Manufacturers in China
Cast Iron Surface Inspection Plate Factory: The Importance of Quality InspectionWhen it comes to manufacturing and testing equipment, quality and precision are of the utmost importance. In industries such as automotive, aerospace, and construction, precise measurements and accurate testing are essential. This is where cast iron surface inspection plates come into play.Cast iron surface inspection plates are designed to provide a flat, stable, and smooth surface for use in measuring equipment and machinery. They are used for a variety of purposes, such as testing the accuracy of machines, checking the flatness of surfaces, and measuring the thickness of objects.But not all cast iron surface inspection plates are created equal. The quality of these plates can vary depending on the manufacturer and the materials used. This is why it is important to choose a reputable Cast Iron Surface Inspection Plate Factory.At a reputable factory, the plates are manufactured with high-quality materials and undergo rigorous testing and inspections to ensure they meet the highest standards. Casting is done in state-of-the-art facilities, and the composition of the iron is carefully controlled to ensure consistent quality.One of the key factors that affect the quality of cast iron surface inspection plates is the composition of the iron. High chromium white iron is used for wear-resistant castings, while cement polished board carbon and silicon content is low. Carbon mainly exists in cementite form, and the fracture surface is carefully analyzed to identify the manufacturing process and any potential defects.Another important factor to consider is the finishing of the plates. The surface must be perfectly flat and free from any defects or irregularities. Advanced techniques such as lapping and measuring ensure that the plates meet exacting standards.In addition to providing high-quality cast iron surface inspection plates, reputable factories also offer customized solutions to meet the specific needs of customers. This includes plates of different thicknesses, sizes, and shapes, as well as special coatings and finishes.In conclusion, choosing a reputable Cast Iron Surface Inspection Plate Factory is crucial for ensuring the highest quality and precision in manufacturing and testing equipment. With the right materials and manufacturing processes, cast iron surface inspection plates can provide the reliable and accurate measurements that industries depend on.
High-Quality Granite Base for Precision CMM Systems
As a world-renowned manufacturer of precision measurement solutions, {company name} continues to lead the industry with its innovative products and cutting-edge technology. One of the company's flagship products, the precision CMM base granite, has quickly become a go-to choice for companies seeking the highest level of accuracy and reliability in their metrology systems.The precision CMM base granite is an essential component of coordinate measuring machines (CMMs), which are widely used in industries such as automotive, aerospace, and medical manufacturing for quality control and inspection purposes. The stability and flatness of the CMM base are crucial for ensuring the accuracy of the measurements taken by the machine, and {company name}'s granite bases are known for their exceptional precision and durability.Manufactured with the utmost attention to detail, {company name}'s precision CMM base granite is made from high-quality black granite that is sourced from the finest quarries around the world. The granite is meticulously machined and hand-finished to achieve a surface finish that meets the most stringent industry standards. This level of craftsmanship ensures that the granite base provides a stable and reliable platform for CMMs to perform at their best.In addition to its exceptional quality, {company name}'s precision CMM base granite is also available in a wide range of sizes and configurations to accommodate the diverse needs of its customers. Whether a company requires a small base for a benchtop CMM or a large base for a bridge-type CMM, {company name} can provide a solution that meets their specific requirements.The precision CMM base granite from {company name} is also designed to integrate seamlessly with the latest CMM technology, allowing customers to take full advantage of the advanced capabilities of their measurement systems. This includes compatibility with high-accuracy probes, advanced software, and other accessories that enhance the performance and functionality of CMMs.{company name}'s commitment to excellence extends beyond the quality of its products, as the company also offers comprehensive support and service to ensure that customers get the most out of their investment. This includes expert guidance in selecting the right precision CMM base granite for a particular application, as well as ongoing maintenance and calibration services to keep the equipment operating at peak performance.With a global network of distributors and service centers, {company name} is able to provide prompt and reliable support to customers around the world. This ensures that companies can trust {company name} as a trusted partner for all their metrology needs, knowing that they will receive the highest level of expertise and service.In a highly competitive and demanding industry, {company name} has consistently set the standard for excellence with its precision measurement solutions. The precision CMM base granite is just one example of how the company continues to push the boundaries of what is possible in metrology, and it is no surprise that companies worldwide turn to {company name} for their most critical measurement challenges.
Top 10 Custom Cast Iron Parts for Various Applications
Customized Casting Iron Parts: Breaking Ground in Industrial SolutionsIndustrial production is continually evolving, requiring exceptional engineering to ensure quality and efficiency. In today’s manufacturing industry, custom casting iron parts have become a popular solution in enhancing the performance of varied machines and equipment. These parts are widely used due to their versatility, durability, and flexibility, as they can be shaped into almost any desired shape and form depending on the specific needs of the device. Thanks to their popularity, Customized Casting Iron Parts have become the go-to for industrial engineers for their diverse applications. Industrial companies seeking to enhance their production should consider partnering with leading firms like {insert company name}, to take advantage of the benefits that cast iron offers. {insert company name} has built a reputation as a leader in the manufacture and supply of Cast Iron Products specializing in unique, customized designs that meet the demands of different industrial applications.At {insert company name}, casting iron parts are an essential component of their diverse product line, which has been refined over the years to meet industry standards. The company not only provides off-the-shelf casting iron components but also offers custom fabrication that ensures clients get parts that are unique to their requirements. This personalized approach enables industrial enterprises to optimize their machine performance to achieve their goals.The advantages of Customized Casting Iron Parts are undeniable. Cast iron is well-known for its high tensile properties, which are useful in applications where the component is subject to significant wear and tear. It is also resistant to heat, has excellent fluidity, and offers exceptional machinability. Additionally, cast iron can be produced to precise specifications, resulting in parts that are of uniform quality and durability.{insert company name} boasts a wide range of customized casting iron parts, including Flywheels, Valve Bodies, and Gears. Flywheels serve as vital components of generators and engines and are designed according to the specific needs of the machine. Cast iron valve bodies are sought after for high-pressure industrial applications as they offer excellent sealing properties and can withstand extreme temperatures. Gears, which can suffer greatly from wear and tear, benefit from the durability and high strength offered by cast iron.Customized casting iron parts are not only durable but also cost-effective. With careful design and engineering, casting iron parts can be optimized for performance, reducing energy waste and increasing cost-efficiency. The high strength of cast iron also eliminates the need for frequent replacements, which can save industrial enterprises money in the long run.{insert company name} utilizes advanced technology and processes to produce the highest quality casting iron parts in volume. With the skilled support of {insert company name} experts, clients benefit from recommendations and guidance on ideal materials, design, and machining processes that optimize their custom parts’ performance.{insert company name} is known for its commitment to customer satisfaction and quality control. Each custom cast iron part undergoes stringent testing to ascertain that it meets or exceeds industry standards. The company employs advanced quality control measures throughout the entire production cycle, starting from the design stage to the finished product to ensure that your requirements are met.The importance of Customized casting iron parts in industrial settings cannot be overstated. Appropriate selection and implementation of these parts can significantly enhance the efficiency and productivity of any industrial operation. With {insert company name}, you are guaranteed top-quality cast iron products that are uniquely designed to meet your specific needs. In conclusion, {insert company name} has set an exemplary standard with their production of custom casting iron parts that enable industrial enterprises to achieve their production goals efficiently. Their expertise, customization, and high-quality standards have made them a top choice for those seeking to utilize customized casting iron parts in their business. If you are considering enhancing your industrial operation’s productivity and efficiency, partnering with {insert company name} is the ideal option.
Revolutionizing Welding: The Latest Innovations in 3D Welding Tables
Title: Leading Welding Table Manufacturer Revolutionizes the Industry with 3D TechnologyIntroduction:Innovation in the welding industry has taken a significant leap forward as a renowned welding table manufacturer introduces cutting-edge 3D technology to their production process. This groundbreaking development ensures improved efficiency, accuracy, and convenience for welders worldwide.With their commitment to continuous improvement and groundbreaking solutions, the company aims to transform the welding experience and set a new standard in the industry. By leveraging 3D technology, they have revolutionized the manufacturing process, enhancing welding tables' quality while reducing production time and costs.3D Welding Table Manufacturer Redefines Quality and Precision:The integration of 3D technology into the manufacturing process allows the company to create welding tables with unparalleled precision and quality. Through the use of computer-aided design (CAD) software and advanced additive manufacturing techniques, they can develop intricate weld fixtures and complex geometries that were previously challenging to achieve.This newfound precision enables welders to improve their workmanship by providing optimal support and stability during the welding process. The 3D tables' superior flatness guarantees quality welds, as the surface ensures the components being worked on remain securely in position, minimizing distortion.Streamlining Work Processes:Not only does the incorporation of 3D technology enable the creation of high-quality welding tables, but it also streamlines work processes for welders. By implementing automated manufacturing processes, the company significantly reduces the time required to produce welding tables while increasing their production capacity.Moreover, the ability to customize welding tables based on welders' specific requirements adds a new level of versatility. Welders can now request tables with unique dimensions, fixture placement, or even integrated clamping systems, ensuring that their equipment perfectly suits their welding needs. This customization not only enhances the welding experience but also boosts overall productivity.Sustainable and Environmentally Friendly Initiatives:In addition to enhancing welders' efficiency and productivity, the 3D welding table manufacturer is also committed to sustainable and environmentally friendly initiatives. By adopting 3D printing technology, they reduce material waste during production considerably. This eco-conscious approach aligns with their vision of minimizing their carbon footprint and contributing positively to the environment.Furthermore, the company utilizes durable, high-quality materials in the production of their welding tables, ensuring longevity and reducing the need for frequent replacements. This sustainable manufacturing approach not only benefits the environment but also enhances welders' operational efficiency by providing robust and long-lasting equipment.Customer-Centric Approach:The company's commitment to customer satisfaction is reflected in their customer-centric approach. They understand that every welder has unique requirements and aims to provide individualized solutions, exceeding customer expectations.Through tailored customer support and after-sales services, they ensure that welders have access to continuous assistance throughout their welding journey. This aspect of their business sets them apart from competitors, as they prioritize creating lasting relationships with their customers.Future Prospects and Expansion:With the successful integration of 3D technology into their welding table manufacturing process, the company is poised for growth and expansion. Beyond gaining recognition within the welding industry, they foresee potential collaborations with other industry players interested in adopting their groundbreaking technology.Additionally, they plan to further enhance their product range by exploring advanced technologies such as artificial intelligence (AI) and Internet of Things (IoT) applications. These advancements will undoubtedly contribute to empowering welders and further improving their overall welding experience.Conclusion:As the welding industry continues to progress, the incorporation of 3D technology in the manufacturing process significantly impacts its future. This innovative welding table manufacturer has taken a bold step forward in revolutionizing the industry, transforming the way welders work. With their commitment to quality, precision, and sustainability, they have set a new standard for the industry, providing welders worldwide with efficient, reliable, and customized solutions.
Advanced 3D Welding Tables for Modular Projects
Introducing a Revolutionary New Solution for Welding: 3D Modular Welding TablesWelding is a critical process in the manufacturing industry, and having the right equipment is essential for achieving high-quality results. That's why [Company Name] is proud to introduce a groundbreaking new solution for welding: 3D Modular Welding Tables. These innovative tables are set to revolutionize the way welding is done, offering unparalleled versatility, precision, and efficiency.[Company Name] has been a leader in providing cutting-edge solutions for the welding industry for over a decade. With a focus on innovation and quality, the company has continuously strived to develop products that meet the evolving needs of welders and fabricators. The introduction of 3D Modular Welding Tables is a testament to [Company Name]'s commitment to pushing the boundaries of what's possible in welding technology.The 3D Modular Welding Tables are designed to provide a comprehensive and flexible solution for a wide range of welding applications. Utilizing advanced 3D modeling and precision engineering, these tables offer unmatched accuracy and repeatability, ensuring that every weld is performed with the utmost precision. The modular design allows for easy customization, enabling welders to configure the tables to suit their specific needs and project requirements.One of the key features of the 3D Modular Welding Tables is their adaptability to various welding methods, including MIG, TIG, and Stick welding. This versatility makes these tables suitable for a diverse range of projects, from small-scale fabrication to large-scale industrial processes. Additionally, the tables are equipped with advanced clamping and fixturing systems, providing secure and stable support for workpieces of any size and shape.Moreover, the 3D Modular Welding Tables are constructed using high-quality materials that are built to withstand the rigors of the welding environment. The robust construction ensures durability and longevity, making these tables a wise investment for any welding operation. Furthermore, the tables are designed to be user-friendly, with intuitive controls and ergonomic features that make them easy to operate and maintain.In addition to their practical benefits, the 3D Modular Welding Tables also offer significant advantages in terms of efficiency and productivity. By streamlining the welding process and providing a stable and adaptable work surface, these tables can help welders complete their projects faster and with greater precision. This not only saves time and labor costs but also improves the overall quality of the finished welds.[Company Name] is committed to providing comprehensive support for its customers, and the introduction of the 3D Modular Welding Tables is no exception. In addition to offering high-quality products, the company also provides training and technical assistance to ensure that welders can make the most of their investment. This includes comprehensive instruction on using the tables effectively and efficiently, as well as ongoing support for any maintenance or troubleshooting needs.The introduction of 3D Modular Welding Tables represents a significant milestone for [Company Name] and the welding industry as a whole. With their unmatched precision, versatility, and efficiency, these tables are set to redefine the standards for welding equipment. Whether for small-scale fabrication or large-scale industrial projects, these tables offer a comprehensive solution that cater to the diverse needs of welders and fabricators.In conclusion, the introduction of 3D Modular Welding Tables marks a new era in welding technology, and [Company Name] is proud to be at the forefront of this exciting development. With their advanced features, user-friendly design, and comprehensive support, these tables are poised to become an indispensable tool for welders around the world. Whether for improving the quality of welds or streamlining the welding process, the 3D Modular Welding Tables are a game-changer that is sure to benefit the entire welding industry.
Discover the Benefits of a Cast Iron Lapping Plate for Superior Surface Finishing
Cast Iron Lapping Plate Enhances Precision and Efficiency in Material PolishingPrecision in material polishing plays a crucial role in numerous industries, ensuring the final products meet the highest standards of quality. To address this need, an innovative company has introduced a state-of-the-art Cast Iron Lapping Plate that promises to improve precision and efficiency in the material polishing process.Manufactured with cutting-edge technology, the Cast Iron Lapping Plate is revolutionizing material polishing, providing a robust and reliable solution for industries involved in manufacturing, research, and development. This advanced equipment is designed to meet the ever-increasing demands of industries where precision is of utmost importance, such as aerospace, automotive, electronics, and medical devices.The Cast Iron Lapping Plate is made from high-quality cast iron to ensure optimum performance and durability. It features a perfectly flat surface, meticulously designed to provide superior flatness and parallelism. This exceptional accuracy enables efficient and precise polishing of various materials, ranging from metals, ceramics, plastics, and composites.The lapping plate is available in different sizes and configurations, catering to the diverse needs of different industries. With its customizable options, companies can select the appropriate specifications that meet their specific requirements. Furthermore, the plate can be easily integrated into existing material polishing setups, minimizing downtime and maximizing productivity.One of the key advantages of the Cast Iron Lapping Plate is its exceptional stability and stiffness. The rigidity of this plate prevents any deformation or distortion during the polishing process, ensuring consistent and uniform results. This stability also extends the lifespan of the plate, reducing the need for frequent replacements and saving costs for companies in the long run.The Cast Iron Lapping Plate also boasts excellent thermal conductivity, allowing efficient heat dissipation during intensive polishing operations. This feature prevents overheating and reduces the risk of material damage, enhancing both safety and productivity. Additionally, the plate's superior material composition renders it highly resistant to wear, reducing maintenance requirements and enhancing longevity.Furthermore, the company behind this innovative lapping plate has established a reputation for delivering high-quality products and exceptional customer service. With decades of experience in the industry, their team of experts is committed to providing comprehensive support and guidance to customers.In addition to supplying cutting-edge equipment, the company offers maintenance and repair services, ensuring that the Cast Iron Lapping Plate continues to operate at peak performance throughout its lifecycle. They also provide training programs and workshops for operators, empowering them with the necessary knowledge and skills to maximize the efficiency and effectiveness of the lapping plate.The introduction of the Cast Iron Lapping Plate is expected to revolutionize the material polishing industry by enhancing precision and efficiency. Its unparalleled flatness, stability, and durability make it an indispensable tool for industries that prioritize accuracy in their manufacturing processes.As industries strive for excellence and constantly push the boundaries of innovation, the demand for high-precision material polishing solutions will continue to grow. With the introduction of the Cast Iron Lapping Plate, companies can now achieve unparalleled levels of precision while optimizing productivity, setting new benchmarks for quality in their respective sectors.In conclusion, the Cast Iron Lapping Plate is set to redefine material polishing standards, promising enhanced precision, efficiency, and longevity. With its exceptional features and the company's dedication to customer satisfaction, industries can now trust in a reliable and cutting-edge solution for their material polishing needs.
3D Worktable Made from Cast Iron: All You Need to Know
Cast Iron 3D Worktable Redefines Precision and Efficiency in Industrial ManufacturingIn the world of industrial manufacturing, precision and efficiency are two crucial elements that can make or break an operation. With the rapid advancement of technology, manufacturers are constantly on the lookout for tools and equipment that can help them achieve higher levels of precision and efficiency in their production processes.Enter the Cast Iron 3D Worktable, a revolutionary piece of equipment that has been making waves in the industrial manufacturing industry. Developed by {company name}, a leading provider of industrial machinery and tools, the Cast Iron 3D Worktable is redefining the way manufacturers approach their production processes.At the heart of the Cast Iron 3D Worktable is its innovative design and construction, which is centered around a solid cast iron base. This provides unparalleled stability and rigidity, allowing for precise and accurate machining operations. In addition, the worktable is equipped with advanced 3D technology, which enables manufacturers to achieve complex and intricate machining tasks with ease.One of the key features of the Cast Iron 3D Worktable is its modular design, which allows for easy customization and adaptation to various machining applications. Whether it's milling, drilling, grinding, or any other machining operation, the Cast Iron 3D Worktable is versatile enough to handle a wide range of tasks, making it an indispensable tool for manufacturers across different industries.Moreover, the Cast Iron 3D Worktable is designed for seamless integration with CNC machines, allowing for automated and precise machining operations. This not only boosts efficiency but also minimizes the margin for error, resulting in higher-quality finished products.In addition to its technical specifications, the Cast Iron 3D Worktable is also lauded for its user-friendly interface and intuitive controls, which make it accessible to both seasoned machinists and those new to the trade. This ensures that manufacturers can harness the full capabilities of the worktable without facing a steep learning curve.Furthermore, the Cast Iron 3D Worktable is backed by {company name}'s commitment to quality and reliability. With a solid track record in providing cutting-edge industrial machinery and tools, {company name} ensures that the Cast Iron 3D Worktable meets the highest standards of performance and durability, giving manufacturers peace of mind that they are investing in a long-term solution for their production needs.There is no denying the positive impact that the Cast Iron 3D Worktable has had on the industrial manufacturing landscape. By offering a combination of precision, efficiency, and versatility, it has become a go-to tool for manufacturers looking to stay ahead in a competitive market.Speaking about the Cast Iron 3D Worktable, {company name}'s CEO expressed his enthusiasm for the impact it has had on the industry, stating, "We are proud to see the positive reception that the Cast Iron 3D Worktable has received from manufacturers. Its innovative design and advanced capabilities have truly set a new standard for precision and efficiency in industrial manufacturing, and we are thrilled to see the positive impact it is having on our customers' operations."In conclusion, the Cast Iron 3D Worktable has undoubtedly raised the bar for precision and efficiency in industrial manufacturing. Its innovative design, advanced technology, and seamless integration with CNC machines make it a game-changer for manufacturers, setting a new benchmark for machining operations. With {company name}'s commitment to quality and reliability, the Cast Iron 3D Worktable is poised to continue making a significant impact on the industry for years to come.