- Home
- Blog
- Affordable and Effective: Using Floor Tiles as Lapping Plates for Blade and Chisel Flattening
Affordable and Effective: Using Floor Tiles as Lapping Plates for Blade and Chisel Flattening
By:Admin
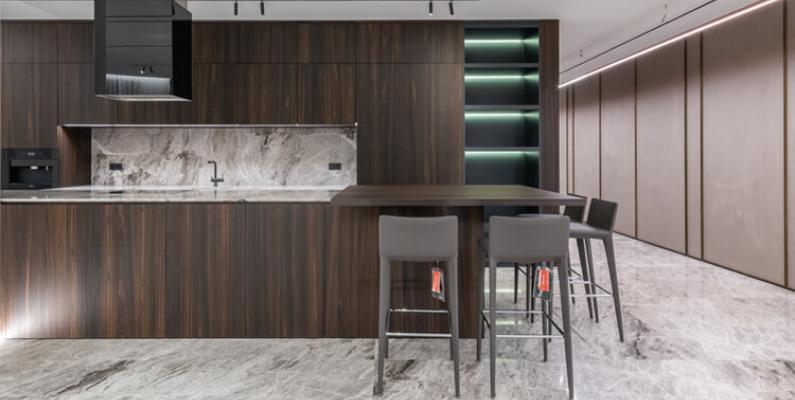
When it comes to woodworking, having sharp tools is essential. Dull blades, chisels or planes can make your woodworking experience frustrating and can leave you with subpar results. That's why it's important to invest in a good quality lapping plate to keep your tools sharp. However, buying a lapping plate can be expensive, which is why we'd like to suggest an affordable solution - using marble or granite tile as a high-quality lapping plate.
Marble and granite tiles are readily available at any home decor or tile store for an affordable price. These tiles are extremely flat and have a smooth surface, providing the perfect platform for sharpening and flattening tools. Plus, they're durable and can withstand wear and tear for years of use. Here's how to use a marble or granite tile as a lapping plate:
Step 1: Prepare your tile
Before using the tile as a lapping plate, make sure it's clean and dry. If there are any marks or scratches on the surface, use a fine-grit sandpaper to sand down the surface until it's smooth.
Step 2: Add abrasive
Apply a small amount of abrasive such as diamond paste or sandpaper. Use a low-grit abrasive to start with, and work your way up to higher grits as needed.
Step 3: Start lapping
Grab your blade, chisel or plane and start lapping. Hold your tool at a consistent angle and apply pressure as you move it back and forth across the plate. This will create an even, flat surface on your blade, chisel or plane.
Step 4: Rinse and repeat
Continue lapping until you've reached your desired level of sharpness. Rinse the tool and tile frequently to remove any excess abrasive and check your work often to ensure you're not removing too much metal from the tool.
In conclusion, using marble or granite tile as a lapping plate can be a cost-effective and efficient way to keep your woodworking tools sharp and in good shape. It's an affordable alternative to expensive lapping plates and delivers the same results. With these simple steps, you can create a smooth and flat surface on your tools and produce excellent woodworking results. So, the next time you need to sharpen your tools, give this technique a try and experience the benefits.
Company News & Blog
Discover the Benefits of Cast Iron in MAGMAinteract for Your Next Cooking Adventure" could be rewritten to "Explore the Advantages of Cast Iron for Your Next Culinary Experience.
Cast Iron V Blocks: Strength and Reliability for Precision MachiningWhen it comes to precision machining, the tools and fixtures used are just as important as the machines themselves. One of the most critical fixtures in machining is V blocks. These special blocks are designed to hold and support round or cylindrical parts during machining.Of all the materials available for making V blocks, cast iron is one of the most popular choices. In this blog, we'll explore the benefits of cast iron V blocks and why they are the ideal choice for precision machining.1. Strength and DurabilityCast iron is a strong and durable material that can withstand the rigors of heavy-duty machining. It is resistant to wear and tear and can handle high-temperature environments without warping or cracking.This makes cast iron V blocks ideal for long-term use and ensures that they will maintain their precision over time. The strength and durability of cast iron also mean that it can withstand the force of high-speed cutting without breaking or distorting.2. Excellent Vibration Damping PropertiesOne of the biggest challenges in precision machining is controlling vibration. Vibrations can negatively affect the part being machined, leading to poor surface finish and alignment issues.Cast iron has excellent vibration damping properties, which means that it can absorb vibrations and prevent them from affecting the machined part. This is crucial for achieving high-precision and high-quality parts.3. Dimensional StabilityCast iron has a high degree of dimensional stability, which means that it maintains its shape and size under varying temperature and humidity conditions. This makes it an ideal material for precision machining fixtures like V blocks, which need to maintain their accuracy across a range of working conditions.Cast iron V blocks are also resistant to expansion and contraction due to temperature changes, which ensures that they maintain their precise alignment with the machined surface.4. Low Coefficient of Thermal ExpansionCast iron has a low coefficient of thermal expansion, meaning that it expands and contracts relatively little as temperatures change. This makes it an ideal material for machining fixtures that need to maintain their precise dimensions across a range of operating temperatures.Cast iron V blocks are particularly useful in high-temperature machining applications. They can withstand the high temperature of cutting tools and prevent any expansion or distortion that could affect the accuracy of the machined parts.5. VersatilityCast iron is a versatile material that can be easily machined to produce a wide range of shapes and sizes. This makes it an ideal material for V blocks, which come in various sizes, from small blocks used for precision measurement to large blocks designed for holding heavy cylindrical parts.ConclusionIn conclusion, cast iron V blocks are an excellent choice for precision machining. Their strength, durability, vibration damping properties, dimensional stability, and low coefficient of thermal expansion make them ideal for high-precision machining applications.If you're looking for high-quality cast iron V blocks for your machining needs, look no further than MAGMAinteract. Our cast iron V blocks are made from the highest quality materials and are designed to provide the strength, reliability, and precision you need for the most demanding machining applications.
DIY Granite Surface Plate: How to Make One with 3 Plates
When it comes to precision machining and measurement, having a reliable surface plate is crucial. While there are various types of surface plates available in the market, granite surface plates are one of the most widely used. However, buying such a plate can be expensive. Hence, some people opt to make their own using the 3 plates method. In this blog, we will discuss what materials are required to make a granite surface plate and the process involved.Materials RequiredBefore we delve into the process, it's essential to have all the necessary materials in place. Here's a list of things you'll need:- 3 surface plates- Epoxy- Two-part epoxy hardener- Sandpaper- LevelThe first step is to purchase three granite surface plates. It's vital that you buy high-quality plates that are flat and have a smooth surface. You don't need brand names when buying these plates; you can get generic ones at a lower price.ProcessOnce you have all the required materials, you can start the process of making your surface plate. Here are the steps involved:1. Clean the surface platesBefore bonding the plates together, ensure that they are clean. You can use a damp cloth to wipe away any dirt and dust particles.2. Level the surface platesUse a level to ensure that all the surface plates are horizontal. If one or two of the plates are not level, it will affect the overall accuracy of the surface plate.3. Prepare the epoxyFollow the instructions on the epoxy packaging and mix the two-part epoxy hardener thoroughly.4. Apply the epoxyApply a 1/8 inch of epoxy evenly on each surface. Be sure to apply it in a thin layer and avoid any air bubbles.5. Put the plates togetherCarefully place the three surface plates on top of each other. Ensure that the plates align correctly.6. Leave it to cureLet the epoxy cure according to the manufacturer's instructions. It usually takes about 24 to 48 hours to cure fully.7. Finish the surface plateOnce the epoxy has cured, use sandpaper to smoothen any rough spots or bumps on the surface. Be gentle when using the sandpaper, so you do not risk damaging the surface plate.8. Test the surface plateBefore using your newly made surface plate, verify its accuracy using a dial indicator. If it's not accurate, you may need to repeat the process.Advantages of Making Your Surface PlateMaking your surface plate is a cost-effective alternative to buying one. It's ideal for individuals who require a surface plate for occasional use but can't afford to invest in an expensive one. Making your surface plate also gives you the flexibility to customize it according to your needs.ConclusionIn conclusion, making a granite surface plate using the 3 plates method is achievable. With the right materials and patience, you can create a flat, accurate, and reliable surface plate. As a bonus, you get the satisfaction of knowing that you made something useful with your own hands.
How Machine Tool Bases Made of Cast Iron Are Revolutionizing Industry
Title: Strong and Durable: Cast Iron Machine Tool Base Revolutionizes Manufacturing IndustryIntroduction: In an effort to push the boundaries of manufacturing technology, a pioneering company, synonymous with excellence in engineering, has recently introduced a groundbreaking innovation – the Cast Iron Machine Tool Base. This revolutionary new product promises to significantly enhance the precision, rigidity, and durability of machine tools, paving the way for unparalleled quality in manufacturing processes. Designed to cater to various industrial needs, this cutting-edge development redefines the very core of machine tool stability, setting a new benchmark in the industry.Breaking New Ground in Manufacturing:The introduction of the Cast Iron Machine Tool Base marks a significant milestone in the manufacturing industry. Engineered from the highest quality cast iron, this robust foundation ensures exceptional rigidity and stability during machining operations. Unlike traditional bases made from different materials, the cast iron composition of this innovative product offers superior vibration damping capabilities, allowing for enhanced accuracy and precision in every application.Strength in Structure:One of the key features of the Cast Iron Machine Tool Base is its unrivaled structural integrity. The high-density cast iron foundation guarantees maximum resistance against structural deformation and dampens any external vibrations generated by machining processes. This enables manufacturers to achieve remarkable surface finishes while minimizing tool deflection, resulting in improved part quality and reduced scrap rates.Moreover, the advanced heat dissipation properties of cast iron offer exceptional thermal stability, allowing for prolonged operations without any loss in machining accuracy. By maintaining consistent temperatures during cutting, the Cast Iron Machine Tool Base minimizes thermal expansion and contraction, ensuring stable dimensions of machined parts even under challenging working conditions.Advanced Machinery Integration:The Cast Iron Machine Tool Base has been meticulously designed to seamlessly integrate with a wide range of machinery, catering to diverse industry requirements. Whether it is milling, turning, grinding, or drilling, this adaptable foundation guarantees optimal tool performance, providing a solid platform for machining operations.Leading the Way in Innovation:Recognizing the need for adaptability, the company has also incorporated state-of-the-art technology into the Cast Iron Machine Tool Base. Precision-ground surfaces and advanced bolt-hole patterns allow for easy alignment and quick installation, reducing setup time and increasing productivity. Additionally, the cast iron base is pre-machined, making it ready for immediate use. Its exceptional durability ensures a long product lifecycle and minimal maintenance needs, delivering cost-effective solutions for manufacturers.Environmental Responsibility:In line with contemporary demands for sustainable practices, the Cast Iron Machine Tool Base exemplifies the company's commitment to reducing the carbon footprint in the manufacturing industry. The cast iron composition of the base is recyclable, maximizing the potential for eco-friendly material use. By incorporating this innovation, manufacturers can contribute to a greener future without compromising on performance or quality.Global Impact:The global manufacturing industry is set to witness a transformation with the introduction of the Cast Iron Machine Tool Base. With its unparalleled stability and exceptional technical specifications, this revolutionary innovation has already begun to create waves across industrial sectors. As manufacturers increasingly realize the benefits of this groundbreaking product, its adoption is poised to revolutionize precision engineering on a global scale.Conclusion:Through the introduction of the Cast Iron Machine Tool Base, the company has taken great strides towards redefining manufacturing standards. With its cutting-edge technology, exceptional durability, and widespread adaptability, this groundbreaking innovation is revolutionizing the way machine tools operate. Manufacturers across industries now have access to an indispensable tool that guarantees superior rigidity, precision, and performance, enabling them to deliver products of unparalleled quality to their customers. As the Cast Iron Machine Tool Base finds its way onto factory floors worldwide, the manufacturing industry is on the cusp of a new era of excellence and innovation.
Shop Online Today for Affordable and High-Quality Measuring Tools with Next Day Delivery Available in the UK.
Granite Tools for Measuring: The Perfect Partner for Accurate EngineeringMeasuring tools are an essential element in the world of engineering. Without them, it would be impossible to accurately assess the dimensions, angles, and other aspects that are fundamental to the creation of precise and reliable products. Among the various options available in the market, Granite tools for measuring stand out as a great alternative due to their outstanding properties and benefits.Granite measuring tools are made of natural granite material, which is renowned for its exceptional stability, flatness, and consistent density. Granite is a hard stone that does not warp, rust, or wear easily, making it an ideal option for manufacturing measuring tools that require precise and consistent measurements. Moreover, granite tools offer excellent vibration-dampening capabilities, reducing the impact of external factors that could interfere with the accuracy of measurements.Granite measuring tools come in different shapes and sizes, depending on the specific application. There are granite squares, straight-edges, surface plates, and angles, among others. Each tool has its own unique features that make it suitable for measuring specific aspects of a component or machine. For instance, a granite surface plate is ideal for measuring flatness, parallelism, and straightness, while a granite angle plate is suitable for checking the squareness of a workpiece or machine parts.Granite measuring tools are widely used in various industries, including aerospace, automotive, machining, and metrology, among others. These tools are ideal for precision engineering and are commonly used for the calibration and inspection of other measuring instruments. Granite measuring tools are also used in research laboratories, where the accuracy and reliability of the data collected are critical.One of the most significant advantages of granite measuring tools is their long lifespan. Unlike other measuring tools made of aluminum or steel, granite tools can last for decades without losing their accuracy. With proper care and maintenance, these instruments can serve as a reliable partner for engineers and technicians for years to come, providing consistent and dependable measurements.In conclusion, Granite tools for measuring are a great investment for any engineering company or laboratory that aims to achieve precision and accuracy in their work. With their exceptional stability, flatness, and durability, these tools are ideal for measuring critical components and machines. Furthermore, granite measuring tools offer excellent value for money, as they can last for decades without losing their accuracy. So, if you want to ensure that your products meet the highest standards of quality, consider investing in granite measuring tools today.
and Foundation Repair.Underpinning is an essential part of foundation repair. It is a process that involves strengthening a foundation that has been weakened by factors such as soil settlement, water infiltration, and structural damage. The process is done by adding support to the foundation, making it more stable and secure.The use of underpinning wedges is a common method used in underpinning. The wedges are used to lift and support the foundation, preventing it from further sinking or settling. The process of underpinning can be complicated, which is why it's important to hire professional foundation repair experts.At the May 21st, 2007 dinner meeting hosted by the New York chapter of the ASME Met Section, Gerard Hillenbrand, P.E. discussed everything attendees always wanted to know about underpinning but were afraid to ask. He provided valuable information about the underpinning process, including when it is needed, the different methods used, and the benefits of underpinning.Underpinning is typically done when a foundation has experienced significant damage, such as cracks or settling. It's important to address these issues before they worsen and cause further problems. Underpinning is also necessary when there is a need to add new floors to a building or to increase the load capacity of an existing foundation.There are several methods used in underpinning, including the use of underpinning wedges. Other methods include pile underpinning, beam and base underpinning, and mass concrete underpinning. A foundation repair expert can determine which method is best for a particular situation.The benefits of underpinning are numerous. It can prevent further foundation damage, stabilize the foundation, and increase the load capacity of the foundation. Underpinning can also be used to level a foundation that has settled, making the building safer and more comfortable for occupants.In conclusion, underpinning is an important part of foundation repair. It involves strengthening a foundation that has been weakened by various factors. The use of underpinning wedges is a common method used in underpinning, and there are various other methods used as well. The benefits of underpinning include preventing further foundation damage, stabilizing the foundation, and increasing the load capacity of the foundation. If you are experiencing foundation issues, it is important to hire a professional foundation repair expert to assess the damage and recommend the best course of action.
Surface Plates: The Ultimate Precision Tool for Accurate Measurements A surface plate is a flat and solid plate used as a reference plane in the precision measurement process. It is commonly made from granite, cast iron, glass, or metal. Granite surface plates are highly preferred due to their superior performance. They are used for a range of applications such as inspection, marking, and quality control. Whether you are in the manufacturing, engineering, or scientific field, a surface plate is an essential tool for accurate measurements.
Surface plates are an essential tool for precision measurement in various industries such as manufacturing, engineering, and quality control. These large, flat plates provide a stable and accurate reference plane for measuring the flatness, straightness, and squareness of objects.Among the different materials used for surface plates, granite stands out as the best choice due to its excellent dimensional stability, high stiffness, and resistance to wear and corrosion. Granite surface plates are made from natural stone that is carefully selected, cut, and polished to achieve a high degree of flatness and surface finish.The quality of granite surface plates is crucial for the accuracy of measurements. A high-grade granite surface plate should have a flatness tolerance of less than ±0.0001 inch over its entire surface. This level of precision ensures that any object placed on the surface plate will be measured accurately, with minimal deviation from the true dimensions.One of the main uses of surface plates is inspection. Metrologists and quality control specialists use surface plates to check the dimensional accuracy of machined parts, gauges, and other tools. They also use surface plates to perform geometric measurements such as parallelism, perpendicularity, and concentricity.Another important application of surface plates is marking. Engineers and machinists use surface plates as a reference surface for laying out patterns, drilling holes, and machining features with high precision. The flatness and stability of the surface plate ensure that the marks or features will be placed in the correct location, with minimal deviation from the design specifications.In summary, a quality granite surface plate is an indispensable tool for accurate and reliable measurement in various industries. Its unique properties make it an ideal reference plane for inspection, marking, and other precision applications. If you want to ensure the highest level of accuracy in your measurements, invest in a high-quality granite surface plate today.
Top Cast Iron Test Bed Plate Manufacturers and Suppliers in India - Verified List Available at Exporthub
India Cast Iron Test Bed Plate Manufacturers and SuppliersIndia has been one of the leading countries in the manufacturing and exporting of various industrial products. One of such products that India has gained enormous expertise and experience in over the years is cast iron test bed plates. Cast iron test bed plates are used in the mechanical and automotive industries to test the accuracy and flatness of various tools and machines. The quality of these cast iron test bed plates determines the accuracy and precision of the machines used in these industries.India has many manufacturers and suppliers of cast iron test bed plates. Let’s take a look at some of the top cast iron test bed plate suppliers from India.1. C. S. Machine Tools: C. S. Machine Tools is one of the leading manufacturers and suppliers of cast iron test bed plates in India. They have a wide range of products that cater to the needs of various industries. They provide customized solutions to their clients based on their specific requirements.2. Optical Flat: Optical Flat is a manufacturer and supplier of cast iron test bed plates based in Mumbai, India. They have over 30 years of experience in manufacturing high-quality cast iron test bed plates that are used in various industries. They specialize in providing customized solutions to their clients.3. Neco Castings: Neco Castings is a manufacturer and supplier of cast iron test bed plates based in Jaipur, India. They have been in the business for over 10 years and have extensive knowledge and expertise in manufacturing high-quality cast iron test bed plates. They provide customized solutions to their clients based on their specific requirements.4. Prakash Engitech: Prakash Engitech is a manufacturer and supplier of cast iron test bed plates based in Rajkot, India. They have been in the business for over 15 years and have extensive knowledge and expertise in manufacturing high-quality cast iron test bed plates. They provide customized solutions to their clients based on their specific requirements.5. Servecast Foundry: Servecast Foundry is a manufacturer and supplier of cast iron test bed plates based in Coimbatore, India. They have been in the business for over 20 years and have extensive knowledge and expertise in manufacturing high-quality cast iron test bed plates. They provide customized solutions to their clients based on their specific requirements.In conclusion, India has many manufacturers and suppliers of cast iron test bed plates. These manufacturers and suppliers have extensive knowledge and expertise in manufacturing high-quality cast iron test bed plates that are used in various industries. They provide customized solutions to their clients based on their specific requirements. India has earned a reputation for being a reliable and trustworthy source for cast iron test bed plates.
Cast Iron Surface Plates for Various Industrial Applications
Cast Iron Surface Plates: The Trusted Choice for Quality ManufacturingCast iron surface plates have been a trusted tool in manufacturing for centuries. They provide a flat and stable surface for engineers and machinists to work on, ensuring precision and accuracy in the manufacturing process. At our company, we specialize in manufacturing and exporting top-quality cast iron surface plates to businesses around the world.Our cast iron surface plates come in a variety of sizes and shapes to meet the needs of any manufacturing process. We offer both standard and customized sizes to ensure that our customers get the exact tool they need for their job. Additionally, we can provide grades A, B, and C, depending on the required flatness. Our surface plates can meet the standards of DIN, GB, and IS, as well as other international standards.Our company has a proud history of providing our customers with high-quality products and excellent customer service. We have been in business for decades, and during that time, we have built long-lasting relationships with our customers. Our team of experienced engineers and technicians ensures that each product we manufacture meets the highest standards of quality and accuracy.Our cast iron surface plates are made from high-quality pig iron, which provides excellent stability and durability. The plates are heat-treated for longer life, and they undergo rigorous quality control processes to ensure that they meet the strictest manufacturing standards. Our surface plates are designed to withstand the wear and tear of heavy manufacturing use and can withstand even the most demanding industrial environments.At our company, we take pride in our ability to customize our cast iron surface plates to meet the unique needs of our customers. We offer a variety of surface finishes, including hand-scraped and ground finishes. Additionally, we can add T-slots, threaded holes, and other features as needed to make our surface plates more versatile and useful for specific manufacturing tasks.At the heart of our business is our commitment to providing our customers with outstanding customer service. We believe that the key to our success is building long-lasting relationships with our customers. Our team of knowledgeable experts is always available to answer any questions or provide guidance on the use and maintenance of our surface plates. We work closely with our customers to ensure that they are getting the right tools for their job and that they are using them to their full potential.In conclusion, cast iron surface plates have been an integral part of the manufacturing process for centuries, and our company is proud to be a leading provider of top-quality surface plates. We offer a wide range of sizes, shapes, and finishes to meet the needs of any manufacturing process. Our commitment to customer service and our dedication to quality ensures that our customers receive the best possible products and support. Contact us today to learn more about our cast iron surface plates and how they can benefit your manufacturing process.
Top Things to Know About Cast Iron Test Plates
Title: Introducing the Revolutionary Cast Iron Test Plate: A Breakthrough in Material Quality EvaluationIntroduction:In the world of manufacturing and engineering, ensuring the quality and performance of materials is paramount. To address this need, a cutting-edge company, known for its dedication to innovation and excellence, has recently introduced a game-changing product called the Cast Iron Test Plate. This revolutionary device has the potential to revolutionize material quality evaluation processes, providing accurate and reliable results. In this article, we will highlight the key features of the Cast Iron Test Plate and its potential impact on various industries.The Cast Iron Test Plate:The Cast Iron Test Plate is a high-precision tool designed to evaluate the quality and integrity of various materials. It serves as a benchmark for testing material strength, hardness, and performance under different conditions. Made from top-grade cast iron, this test plate exhibits exceptional durability and stability, ensuring that it maintains its accuracy over an extended period of use.One of the prominent features of the Cast Iron Test Plate is its exceptional flatness. The surface of the plate is meticulously ground and lapped to achieve extreme precision, guaranteeing consistent and trustworthy results. Its flatness is within a few micrometers, making it an ideal tool for calibrating measurement instruments and verifying the accuracy of testing equipment.Furthermore, this state-of-the-art test plate is engineered with superior dimensional stability, minimizing the possibility of distortion, warping, or any other form of deformation. Its stability allows for accurate and reliable measurements, making it a dependable partner in material quality evaluation processes.Applications across Industries:The Cast Iron Test Plate finds applications across a wide range of industries, including automotive, aerospace, manufacturing, and construction. In the automotive industry, it can be utilized to assess the quality of engine components, brake materials, and suspension parts, ensuring safety and performance standards are met. For aerospace manufacturers, the test plate offers a precise means of evaluating aircraft materials, including structural components and landing gears.Indeed, the Cast Iron Test Plate's versatility extends to the manufacturing sector, where it serves as an invaluable tool for assessing the integrity of molding dies, machined components, and weldments. Construction companies can also benefit from this pioneering technology, as it aids in evaluating the quality of building materials and determining their structural stability.Company Insights:As a leading provider of cutting-edge engineering solutions, {} specializes in the development and production of high-precision measuring instruments. With a focus on research and development, the company has continuously delivered exceptional products that cater to the evolving needs of industries worldwide. Committed to quality and customer satisfaction, the company's dedication to innovation and excellence has garnered it a reputation for being a reliable and trusted industry partner.Conclusion:The introduction of the Cast Iron Test Plate represents a significant advancement in material quality evaluation. With its exceptional precision, flatness, and stability, this revolutionary tool is set to transform the way industries assess the performance and integrity of materials. From automotive to aerospace, manufacturing to construction, the Cast Iron Test Plate offers a reliable solution, ensuring that quality standards are met and exceeded. As companies strive for excellence, embracing innovative tools like this test plate will undoubtedly yield improved efficiency, safety, and overall product quality.